Contact IEL:
IEL inc.,
1 Good Hope
Beterverwagting
East Coast Demerara
Guyana
South America
Tel: +592-20-2314
Fax: +592-20-7733
iel@guyana.net.gy
Photos:
Jonathan Orenstein Studio
WebPages:
Ronan McDermott
IEL inc
| |
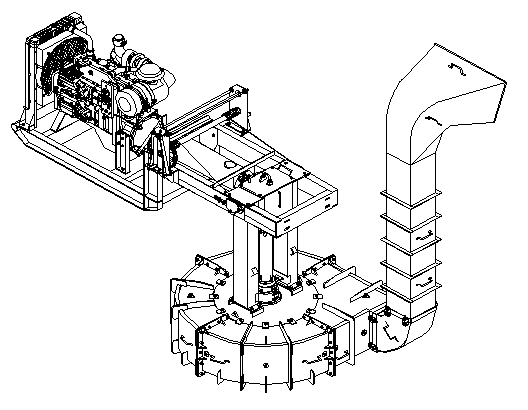 |
General Production Equipment
At IEL we believe that there is the right tool for every job. And since every job is
different, we routinely design most of our tooling on the production floor to suit our
particular needs. The hydraulic components we use are standard and interchangeable so
there is never the problem of availability of parts for repairs or servicing. Some
examples of these are: |
- Beam Processing Line for the production of beams and girders for mezzanine floors in our
steel frame buildings. Consists of:
- 5-Ton Electric overhead crane; as the bay spacing, span and available
work area was unique.
- 100-ton NC Beam Punching Line capable for processing up to 3 tons of
beams per 8 hour day with any center-to-center hole spacing, and a hole diameter of 25mm
in a 20mm thick plate
- 650mm capacity fully automated hydraulic Bandsaw to cut the beams being
processed on our Beam Punching Line.
Plate Decoiler Machine (1500mm width x 12mm capacity). This unit was designed for the
ease of loading coils using the weight of the coil to keep itself in the right position so
that the plate feeds into our own 5 roll decoiler unit. The output height of the plate is
set to feed the plate into a shear with was also completely redesigned to meet our
particular needs.
Plate Slitter Machine (10mm Capacity) with hydraulic drive and fully adjustable plate
width feeder rolls.
Roll Former for producing Industrial Profile Cladding.
Roll Former for producing standard 8" purlins and sheeting rails.
300mm capacity fully automated hydraulic Bandsaw.
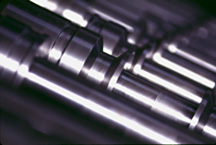 |
Special Project Equipment
In our commitment to the highest quality products, we occasionally build special
machines to enable us to do a job better. Take cane punts for example. To improve design
quality and speed up production we designed and built a machine that will radius flat
steel on edge in one swipe. Then we designed and built another machine to bend two corners
on a plate on flat simultaneously. These two machines allow us to fabricate cane punts
using two half sections thus reducing the number of weld seams from 8 to 2 and improving
the overall quality of the product. |
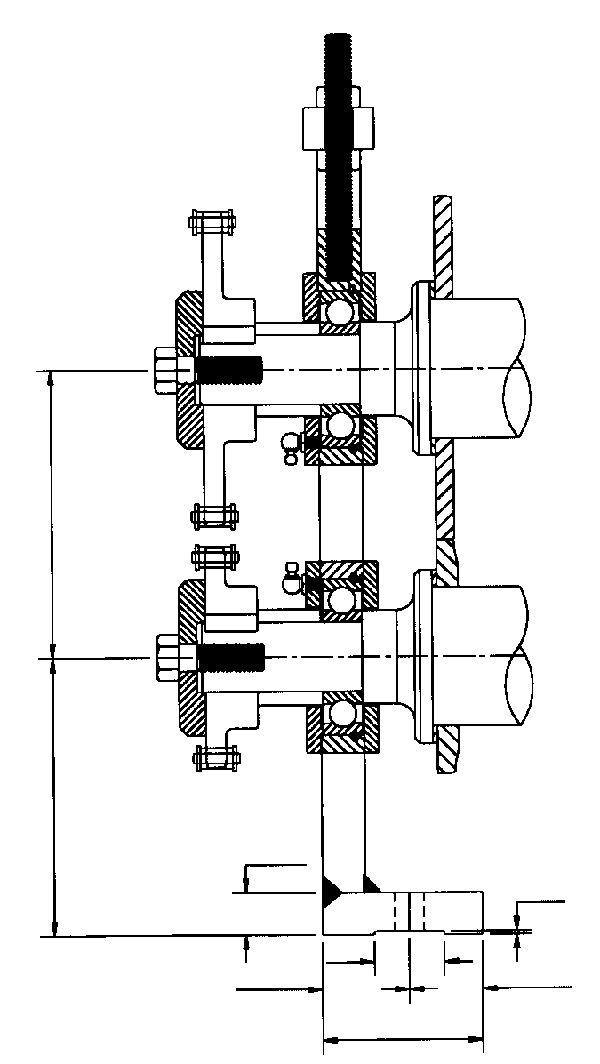 |
The cladding Roll Former was designed and manufactured entirely in
house.
The chassis was assembled in the fabrication department after
which the roller side frames were fabricated and then milled to accommodate the roller
bearing carriers. Their bases were then squared using a shaping machine.
The roller shafts and forming rolls were machined to exacting
standards using CNC machinery. The keyways in the shafts and rolls were machined using a
combination of machines including a milling machine, a shaping machine and a broaching
machine.
The drive system consists of a hydraulic unit (again designed by I.E.L.) which drives
hydraulic motors which in turn drive the rollers via a chain and sprocket system. |
|